Kronos 3
Date Published: 05/29/2024
This project was started around September of 2023. After developing my first quadcopter, I noticed some critical flaws in the design. For example, the aircraft had low maneuverability, loose connections, heavy frame, and low ease of maintenance. I noted the issues and began the development of Kronos 3, a quadcopter that has extended runtime and is significantly more stable. A demo video of the final product is shown below.
To develop the second iteration of the improved quadcopter, I started by designing the
new frame in Autodesk Inventor. I made the entire structure significantly smaller
to reduce the manufacturing time. My plan was to create a 3d printed frame and install
thin aluminum sheets on the top of the quadcopter to reduce arm defelction when in motion.
For Design for Assembly (DFA) considerations, the arms had alignment notches for ease of
installation.
This quadcopter has a 3-axis gimbal. The previous version of the aircraft had a gimbal
as well but had significant backlash between the gears. To solve this issue, I designed
and printed double helical gears which meshed very well together. I had to reference the
motor spec sheets to ensure there was enough torque to overcome the additional friction these
gears usually have.
Due to FAA regulations, quadcopters must be equipped with a flashing strobe light when flying during twilight hours. For this reason, I designed a custom circuit that flashes a 10W led chip once every second. I decided to use a 555 timer with a mosfet for led control Then, I calculated the optimal resistor and capcitor values for the desired frequency of the 555 timer. One of the problems I encountered when designing the strobe assembly was heat dissipation. Some of my prior designs had the led strobing at a higher frequency. This caused the led to dissipate more heat and draw more power causing a reduction in flight time. To combat this, I reduced the frequency and added a large heat sink to the chip.
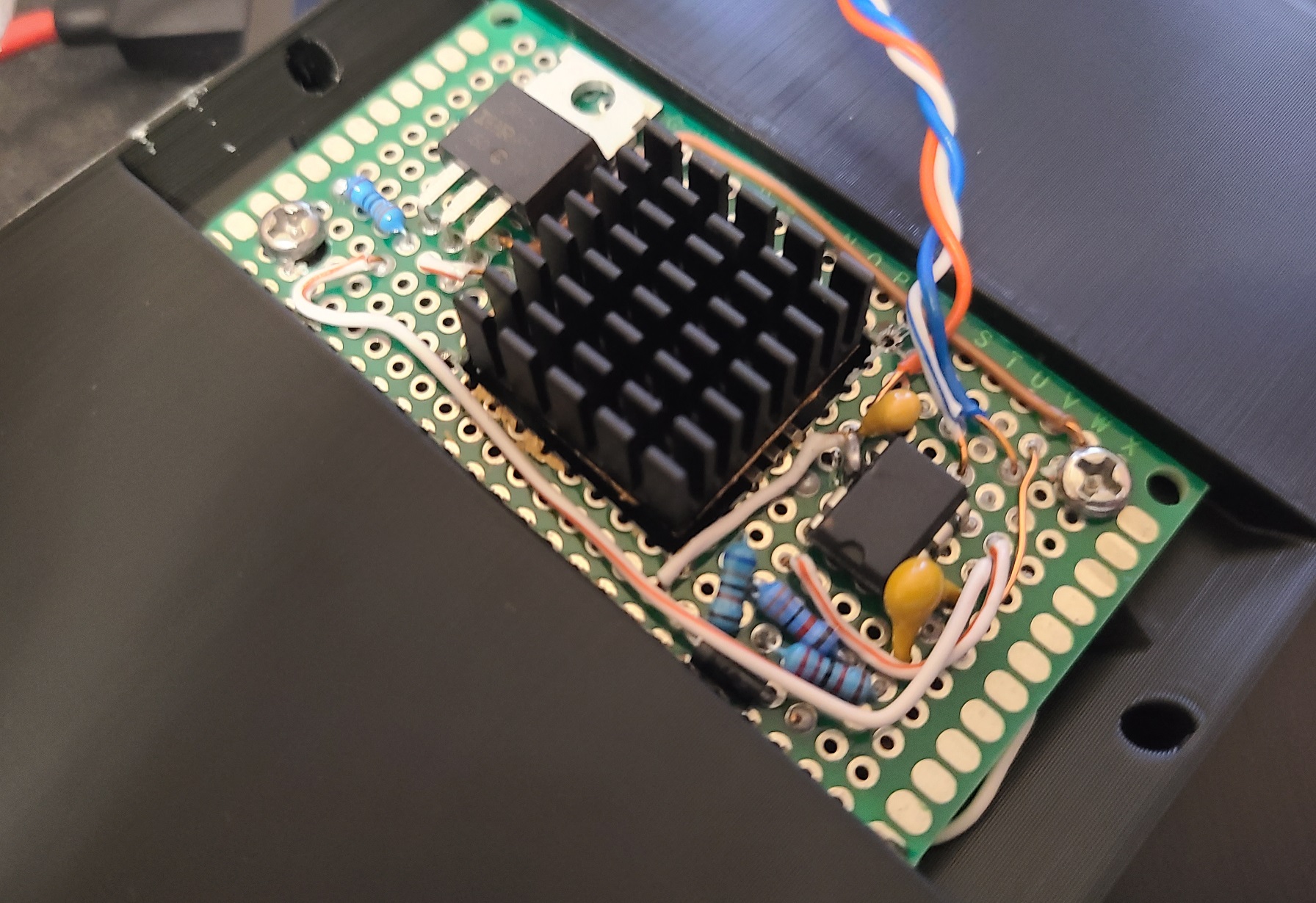
I spent time refining the design around the flight controller and various PCB mounts onboard. In the past, I forgot to account for the wires and rigidity of the different connectors. I learnt from my mistakes and improved my modeling skills when working with PCB's and electrical components.
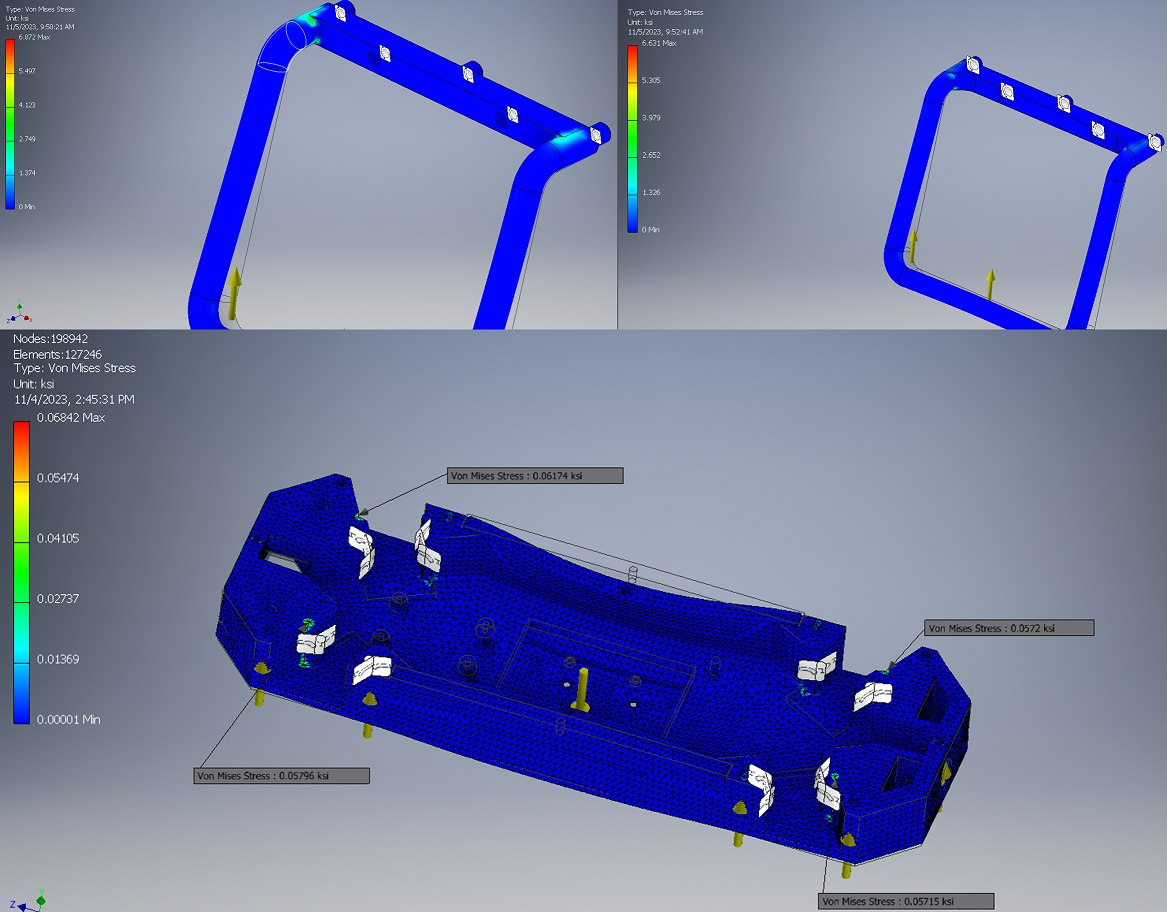
When starting this project, the total weight was around 5 lbs. After performing
FEA simulations on the different components, I was able to remove material from the body to
reduce the final weight to 4.6 lbs. Additionally, with the analysis, I added fillets to the landing
legs to reduce the possibility of shear in the event of hard landings. Initially, it was found that
with repeated loading of the legs, failure could occur at the fixture points. After thickening the
edges of the component, stress was able to be distributed over a wider area.
Overall, the Kronos 3 quadcopter was a success. I was able to identify the shortcomings of the previous design
and create a better product. The quadcopter is now easier to fly, maintain, and transport. Furthermore, I
strengthened my engineering knowledge and was able to combine various engineering disciplines to create a working aircraft.